Mobile : +91 9488 444777, +91 94868 58777
Landline : +91 9488 444777
Marine Heat Exchangers Manufacturer INDIA
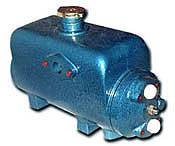
We offer marine heat exchangers, Mercruiser heat exchangers, marine water pumps and other marine cooling systems parts.
We only can assist you in determining the best all around product for your particular application.
Marine heat system are the most common way to cool a boat's engine, using the lake, river or ocean water in which the boat floats. Since this water may be corrosive the engine may be cooled by a sealed mixture of distilled water and antifreeze. Heat from the water-antifreeze mixture is then transferred to the ocean (or lake or river) water which flows into a heat system. The water-antifreeze mixture runs through the heat exchanger dumping heat, but remaining separate from corrosive salts and chemicals found in the water the boat is floating in. If the ocean water eventually corrodes and ruins the heat system it can be replaced at a fraction of the cost of replacing the engine.
To protect the marine heat exchanger from corrosive salts, a sacrificial zinc anode is screwed into the heat exchanger. This anode must be periodically replaced as part of regular maintenance.
Because the water the boat floats in may be contaminated with floating particles such as wood or styrofoam balls the well designed boat will have a filter (often stainless steel mesh) to remove these particles before they are moved toward the heat exchanger. This filter must be periodically cleaned or else the flow of water to the heat exchanger will become obstructed and the engine will overheat.
Ocean water is caused to flow through the heat exchanger by an impeller, often made of rubber and looking like a paddle wheel. Impellers commonly fail by having their paddles fall off and when this happens the engine will overheat unless promptly shut off. Many marine engines using heat exchangers have a grease reservoir for the impeller. In such cases a screw is often made part of the reservoir and is turned a small amount periodically, such as once a month, to apply a bit of grease to the rubber impeller to reduce friction and prolong its life.
A consequence of using a heat exchanger on an in-hull marine engine is that there must be a thru-hull opening below the waterline to admit the ocean water to the marine heat exchanger. Most boats with this arrangement have a valve which closes this hole when the boat is unattended so that a leak in the cooling system will not cause the boat to fill with water and eventually sink.
There are three methods employed for water-cooled marine petrol and diesel engines: direct, heat exchanger and keel cooling. Direct cooling of the cylinders and heads by seawater is unsatisfactory, because the engine – which was probably originally designed for radiator cooling – will run too cold and the sea-water will eventually ruin the cylinder block and heads. Our cooler is suitable for small boats operating in shallow weedy water, but the need for pipe work external to the hull is a severe limitation. Heat exchanger cooling is the most common method, the seawater being isolated in components which can be designed to withstand its corrosive affect.
The closed fresh-water circuit can be thermostatically controlled so that the engine operates at its design temperature. Our heat exchangers are high-quality products incorporating both the best materials and the latest technical features. The tube stack is fully floating, thus minimizing thermal stresses, and it can easily be removed should cleaning be necessary. Our heat exchanger header tanks prevent aeration of the engine water circuit which must be designed so that the system is self-venting on initial filling.
It is usual for all the components in the seawater circuit to be in series, the gearbox-oil and engine-oil coolers being on the suction side of the sea-water pump and the heat exchanger and any sea-water-cooled exhaust manifolds being on the discharge side.
In the case of turbocharged engines the charge air cooler should receive the sea-water first so that the lowest possible air temperature is obtained. The sea-water outlet from the heat exchanger should be from the end cover equipped with the upper connection, this ensures that the tube stack is always full of water. The gearbox cooler size will depend on the type of transmission used, but it will usually be a size smaller than the engine-oil cooler. If preferred, the oil coolers can be fresh-water-cooled; these will need to be larger owing to the higher water temperature but need not be suitable for sea-water and can be taken from our leaflet ENGINE AND TRANSMISSION OIL COOLERS.
A water-jacketed exhaust manifold is necessary on marine engines to reduce the temperature of the engine-room air space and the exhaust pipe. If the exhaust manifold is in the sea-water circuit it should be installed with the sea-water inlet at the back and the outlet at the front on the top to ensure that it operates completely full of sea-water. If the manifold is in the fresh-water circuit a small by-pass hole must be provided in the thermostat to ensure that some water is circulating through the manifold at ail times.
Our development is to combine a water jacketed exhaust manifold with the heat exchanger and header tank. This arrangement is particularly suitable for small series-produced engines; the manifold is cooled by fresh water and as a result a keel-cooled engine can be made by omitting the heat exchanger tube stack and the sea-water pump. On installation the fresh-water outlet from the manifold would be connected to the keel pipes and the return taken back to the engine fresh-water pump. Heat exchanger/manifold assemblies are heavier than ordinary marine manifolds and must therefore be supported on the underside using the fixing lugs provided.
When automotive engines are being converted for marine use the existing centrifugal-type pump should be retained for the fresh-water circuit and an additional pump fitted for the sea-water circuit. The sea water pipe bore should be chosen so that the velocity does not exceed 2 m/sec on the suction side and 3 m/sec on the discharge side of the pump. If the engine is being used to drive auxiliary equipment in a ship and the sea water supply is taken from the ship's main, ensure that the recommended flow rate cannot be exceeded.
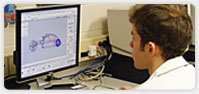
- Home
- Heat Exchanger Manufacturers
- Products
- Contact Us
- Enquiry
- Shell & Tube Heat Exchanger
- U Tube Bundle Heat Exchanger
- Air Cooled Heat Exchanger
- Air Cooled Condenser
- Oil Coolers
- Marine Heat Exchanger
- Kettle Reboiler Type Exchanger
- Double Pipe Heat Exchanger
- Flue Gas Air Preheater
- Plate Finned Heat Exchanger
- Plate Heat Exchanger
- Brazed Plate Heat Exchanger
- Pressure Vessel Manufacturers
- Coil Type Heat Exchanger
- Removable Tube Sheet
- Fixed Tube Sheet
- Tube Bundle Heat Exchanger
- Vertical Shell Tube
- Air Heat Exchanger
- Aluminium Heat Exchanger
- Compact Heat Exchanger
- Copper Heat Exchanger
- Finned Tube Heat Exchanger
- Water Heat Exchanger
- Stainless Steel